
Project Scope.
The client we served requested a completely automated blending system for various grades of raw material in order to provide a high-quality, uniformly standardised output to their customers. Trickle Cassava Solutions proposed a PLC- and SCADA-based comprehensive automation system that enables operations to run smoothly.
Solution
Our team of comprehensive PLC automation system for raw material blending may be programmed. Each of the 16 hoppers, which are outfitted with programmable electronic controllers, is dynamically assigned to each raw material. The programmable mix-and-match creates a range of blends, allowing the company to provide more diversity without sacrificing quality. The roasted raw ingredients are transferred to the relevant hopper via the belt conveyor. The load cell displays the weight of the filling hopper. After the loading is completed, the procedure is transferred to loading the remaining raw materials. When the necessary composition is present in the respective hoppers, blending is initiated. One press of the product name and quantity discharges the raw materials uniformly by opening the pneumatic sliding gates and vibratory system installed at the hopper’s outlet(s). This is accomplished in a regulated manner by adjusting the vibration speed in response to the weight in the load cell. Materials for blending an appropriate composition are delivered to the blender. A single man works at the other end of the belt conveyor to bag the finished product. PLC and SCADA are used to automate the entire system.
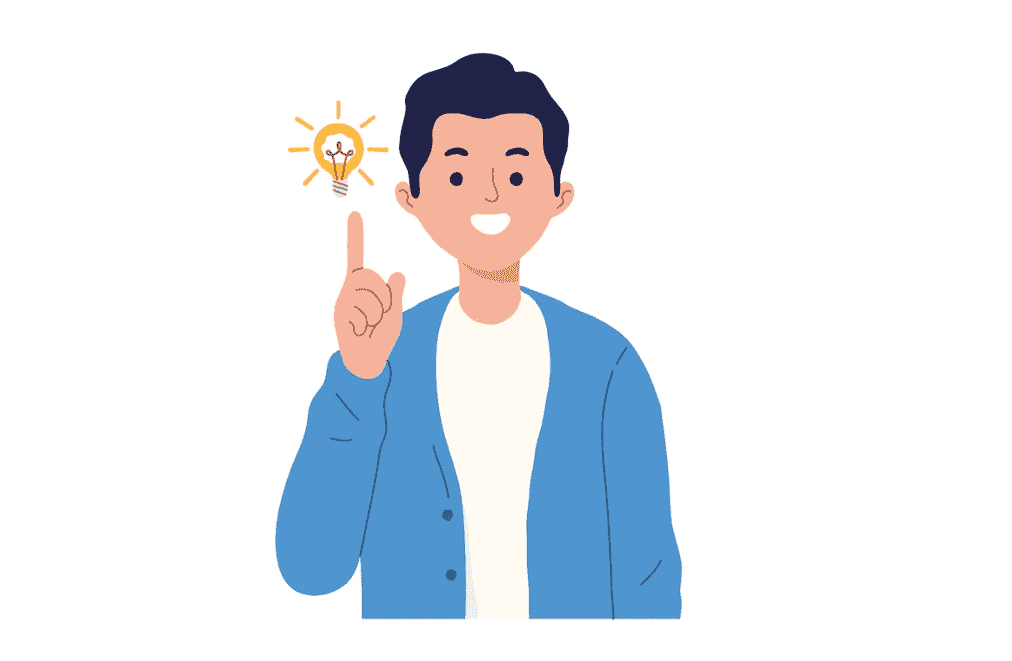

Benefits
Automation led to improved quality. With increased productivity came a significant reduction in the workforce. Customer satisfaction rose as a result of consistently providing the greatest level.