Project Scope
To improve their present layout, the customer requested a single-line process flow that was nicely aligned. The current storage was in gunny bags. There was a need to develop a system that would boost storage and manufacturing efficiency while also ensuring consistent flavor in a high-quality final product. Trickle Cassava Solutions proposed a system that is completely online from the time raw materials are unloaded from trucks until the time processed raw materials are transferred to the next process.

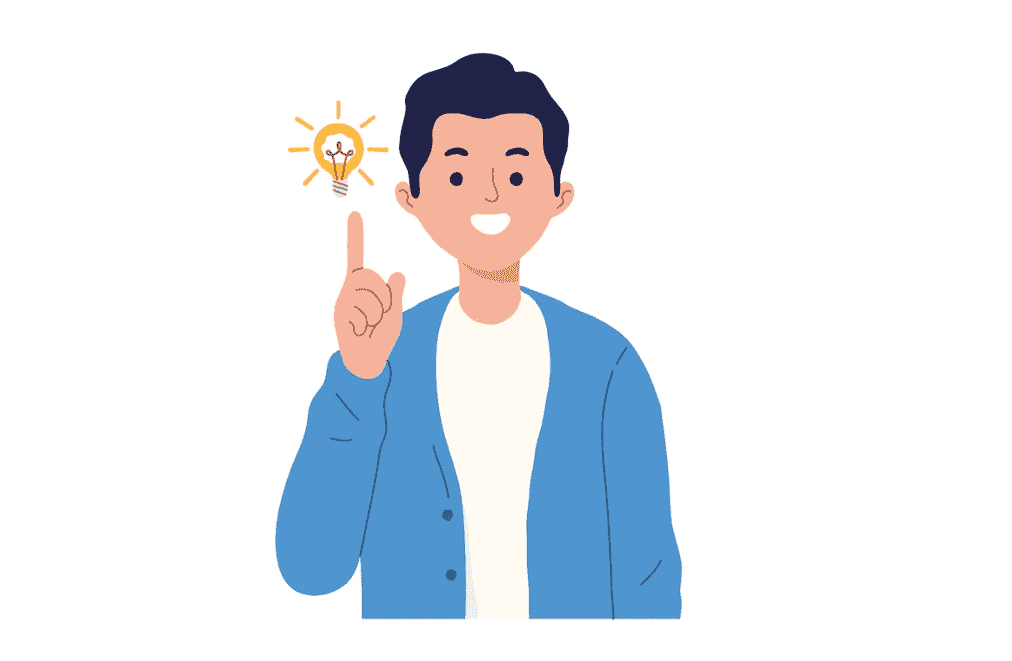
Solution
The system we use includes a 250-ton storage hopper with inlet and outlet bucket elevators to facilitate the flow of beans from trucks. The hopper is divided into compartments so that various raw materials can be filled in each compartment and transferred for processing as needed. Screw conveyors move raw material to the top of the hopper for discharge into the appropriate compartment. Each hopper compartment has a level sensor that detects material filling and controls the incoming stream.
The materials are moved to equal-sized silos equipped with small weighment hoppers at the bottom and high precision load cells to release the beans in the correct composition prior to the important blending procedure. The discharged material is blended and roasted in the processing equipment before being moved to another silo with partitions for the grinding process. The ground material is subsequently transferred to the final destination using a Z-elevator and a belt conveyor.
Bucket elevators and Z elevators are used to transport materials to different procedures. The building materials utilized in all of the equipment are of the greatest quality, meeting the client’s specifications.
Benefits
The whole process was designed such that their everyday production flow was not disrupted at any point in time.
The scientific approach of bulk storage in hoppers and silos reduced the need for gunny sacks, saving half of godown area. Mechanised handling combined with automation reduced handling costs. Perfect material storage and transportation ensured no leakage or waste. The client was able to save significant amounts of manpower while increasing production noticeably.
